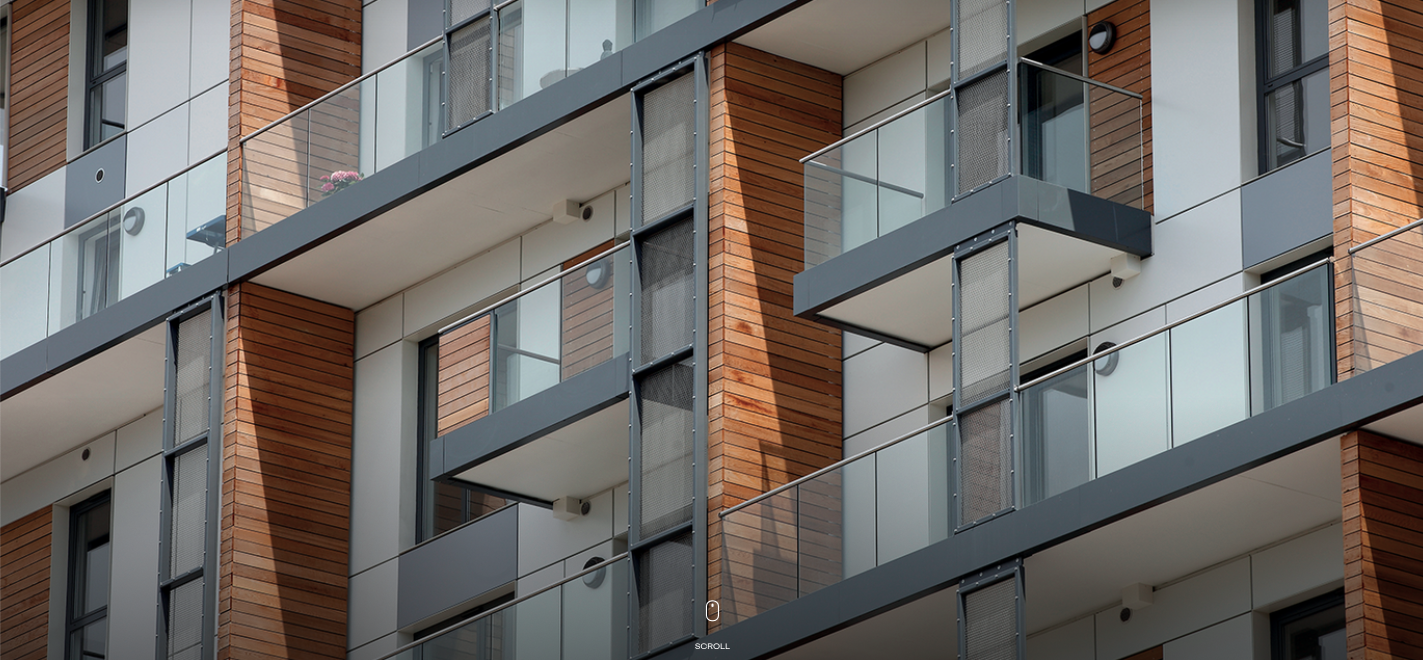
Benefits of powder coating
Negligible VOCs and no air pollution
Powder is recyclable
Minimal hazardous waste
Environmental regulations
Choosing windows and doors for a project is a decision that will nearly endure a lifetime. With endless color and shade possibilities, UV-resistant powder coating provides a durable surface treatment to reduce maintenance. Simple cleaning with some water, a sponge and a neutral, non-scratching soap, will allow the finish to withstand the test of time without having to invest in paint or varnish.
Powder coating is an environmentally friendly way to paint your windows and doors which excludes the use of VOC’s (Volatile Organic Compounds) and requires less energy than many other surface treatments. Similar to anodizing, powder coating is highly resistant against UV radiation and protects against corrosion. In the first step of the powder coating process, the aluminum is degreased, etched and a protective conversion layer is put on the surface. Next, a negative charge is applied on the powder particles, to attach the powder coating to the grounded aluminum. Finally, profiles are cured in an oven in order to polymerize the powder coating into a stable, high quality, scratch resistant finish.
Our Reynaers aluminum windows and doors offer the following ranges of AAMA finishes:
AAMA 2603 (Qualicoat class I): Available in all RAL colors.
AAMA 2604 (Qualicoat class II): Available in a wide range of RAL colors and a series of colors that give an anodized look to your profiles.
AAMA 2605 (Hyper Durable Colors): Available in seven standard colors.
AAMA 2603 and AAMA 2604 color ranges can be delivered in either Matte or Fine Textured finish. AAMA 2605 colors are available in standard Matte finish only. MatteFine textured Reynaers focuses on quality and sustainability, offering all treatments according the American AAMA and certified European Qualicoat standards. For European sourced extrusions, we partner with Axalta Coating Systems to source class Iand class II powder coatings and Oxyplast for hyper durable colors. All products are finished with a minimum 60 microns (2.4mil) of powder, which far exceeds AAMA requirements providing a superior finish coat. Powder coating is performed at Reynaers’ plants in Europe as well as US suppliers audited by Reynaers specialists.